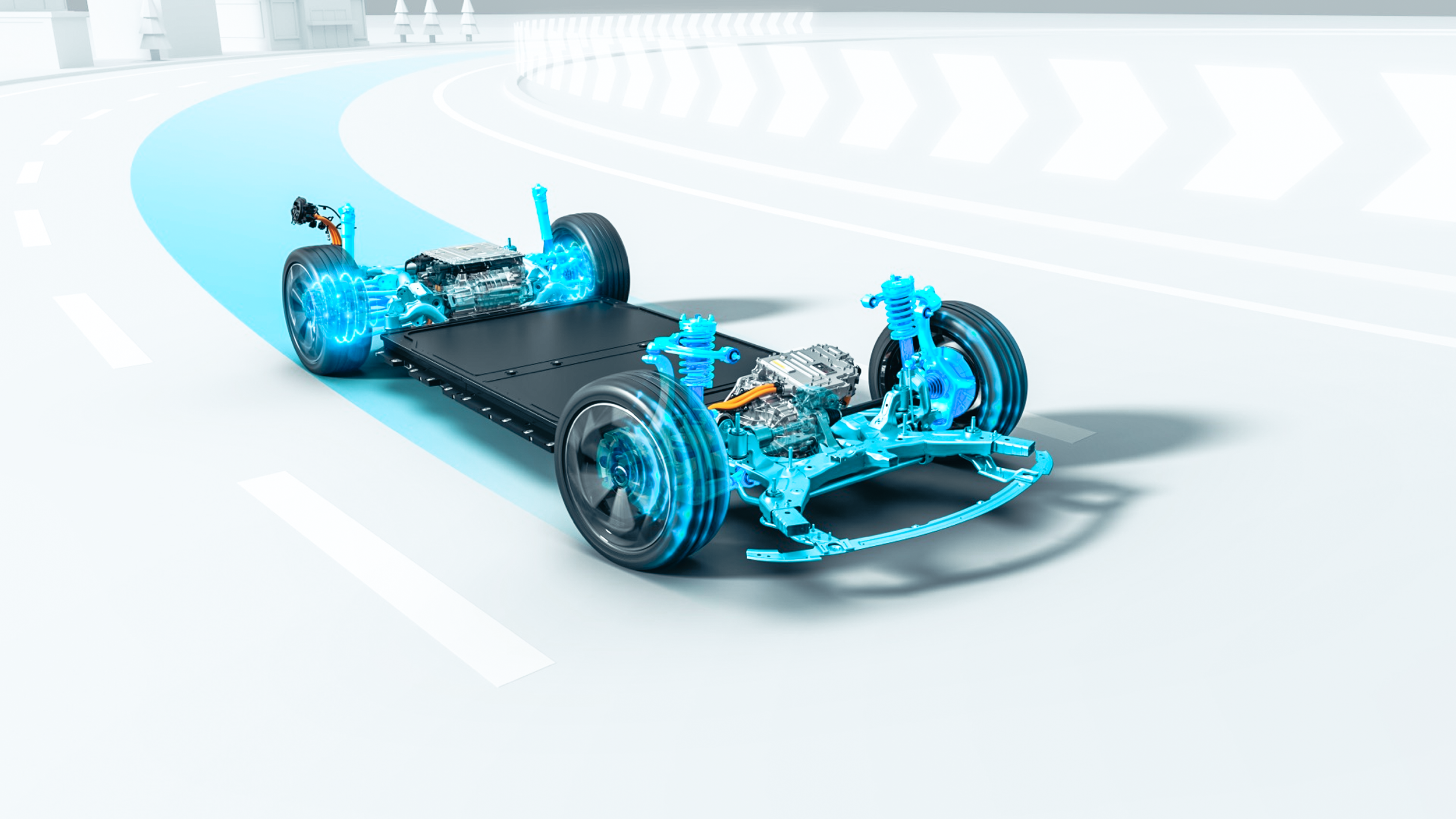
BYD power: what’s special about its batteries?
Words Hazel Southwell | Imagery BYD
Advertising Feature
Car companies don’t, for the most part, manufacture their own batteries. Those that do tend to assemble cells manufactured elsewhere into their own package – what Tesla does with Panasonic cells or Mercedes-Benz with CATL ones, for instance. Not BYD.
BYD’s battery heritage is different because it does develop and make its own battery technologies from the cell level. And it has done since its inception in 1995, when it began making nickel-cadmium rechargeable batteries before branching into lithium-ion cell development the following year.
Within a few years, BYD was supplying Motorola and Nokia smartphone batteries. And today it makes everything from smaller batteries for devices through to enormous energy storage solutions for solar farms. And, of course, car batteries – with a novel chemistry that gives BYD a distinct edge on costs and safety.
The right chemistry
Ternary lithium batteries, so-called because they typically integrate three metals (nickel, cobalt and manganese) in their cathodes, have been the go-to for electric vehicles requiring high energy density and a high number of charge cycles.
But BYD has pursued a different path, embracing lithium iron phosphate (LFP) for the cathode. LFP is more stable, safer and more recyclable, as well as not needing cobalt.
But there’s a snag: it’s typically less energy dense and less good at holding charge capacity in cold temperatures. Both of those things are important for EVs, which is why BYD packages its LFP cells in a clever structure called ‘Blade’, whose appearance resembles the head of a wet shave razor.
Using long, blade-like cells that sit cross-ways across the battery, the packaging is 50% more space-efficient compared to other methods. That puts a lot more cells into a pack, solving the energy density issues and improving charging performance. And LFP’s cold weather performance can be mitigated with a heat pump to efficiently adjust the battery to optimum temperature to enhance range, equipment that’s standard on all UK BYDs.
A BYD’s backbone
The benefit of Blade packaging isn’t just in the number of cells that can be put into a pack. Making batteries is complicated and requires a lot of robot assembly; high voltage systems are dangerous and heavy, so automation is maximised on assembly lines.
So far, so typical automotive industry. But all that means manufacturing batteries can be expensive and inefficient, so any steps that reduce complexity will drive down costs and help make EVs more attainable.
Because of the way the Blade cells are made, they can be pooled in homogenous packs that fit a variety of vehicles. And this is a strength of BYD’s e-platform 3.0, the chassis which underpins three quite different EVs in the compact Dolphin hatch, Atto 3 SUV and longer Seal saloon. Their battery sizes range from 44.9kWh through 60.5kWh to 82.5kWh but all three are Blade and a structural component.
The top of the battery is part of each car’s floorpan, with the battery cells beneath in a tray. That means you can drop out the whole section for servicing or repairs: stand beneath one on a maintenance ramp and you’ll be able to look up through the rectangular hole and see the dashboard and roofliner still in situ. Tesla also uses this structural approach, which BYD calls ‘cell-to-body’ technology – and it has a safety implication too.
Safe, even in a double impact
Using the Blade battery as a structural member boosts vehicle stiffness, which provides a stable platform to tune the suspension dynamics and is great for safety.
Because batteries sit in the floor of an EV and crash loads can be routed around the pack, they’re generally quite well protected in front and rear impacts. Side impacts, however, are much riskier.
In the video below of a double side impact test on a BYD Seal, its Blade battery stayed intact, without electrolyte leakage, fire or deformity. Watch to the end for a nifty reveal of whether the battery still worked.
Critically, the passenger cell stood up to the test too, and the Euro NCAP crash testing regime has awarded both the Seal and Dolphin 89 per cent for occupant safety, amid five-star ratings overall.
BYD nails it
Battery fires have undoubtedly contributed to some of the electric car’s image problems. Whether it’s dramatic images of the car-laden container ship Felicity Ace burning or Chevrolet’s warning not to charge your Bolt EV in the garage, there’s a perception that fires are a major risk.
It’s not borne out by statistics: studies show that EVs are, proportionally, 20-80 times less likely to catch fire than combustion vehicles. Which figures, since engines very much rely on igniting fuel. Nonetheless lithium-ion fires can be devastating, burning at thousands of degrees.
In tests, BYD’s Blade has shown it can withstand being stabbed with a nail. The battery emits no smoke or flames, doesn’t raise its temperature above 60˚C and actually still works. Watch the video below to see a very different result from a nickel-cobalt-manganese lithium battery subjected to the same test…
Safer charging
There are lots of things EV owners can do to look after their batteries, like pre-conditioning for a charge or selecting slower charging to 80 per cent when it’s convenient overnight. But there’ll be times when you need to fill the battery fast though and that’s when cells can be put under strain.
As part of the safety testing for its Blade, BYD subjected a battery to being overcharged by 260%. That’s extremely dangerous territory, every percentage of overcharge causing the battery to generate heat but the Blade system remained intact and didn’t smoke or catch fire.
BYD’s safety goals in developing Blade were to prevent it reacting at very high temperatures and to avoid it generating excessive heat. Both of those contribute to its fire safety credentials, with a third factor of limiting oxygen release also reducing the fire hazard.